Revolutionizing Electric Vehicle Manufacturing With Custom Metal Fabrication: Pioneering a New Era of Automotive Excellence
Electric vehicles (EVs) are at the forefront of the automotive industry’s transformation. The shift toward sustainable transportation has brought new challenges and opportunities, particularly in manufacturing. Custom metal fabrication plays a crucial role in meeting the demands of EV production, providing innovative solutions that enhance vehicle performance, efficiency, and durability.
Corrugated Metals has been a reliable expert in custom metal fabrication for decades! We are committed to producing defect-free products, delivering excellent service, and offering competitive prices to our valued customers.
The Importance of Custom Metal Fabrication in EV Manufacturing
Custom metal fabrication plays a crucial role in EV manufacturing due to several key reasons:
Design Flexibility
EVs often require unique designs to accommodate battery packs, electric motors, and aerodynamic considerations. Bespoke metal fabrication allows manufacturers to create parts and components tailored to these design requirements. This contributes to improved vehicle performance, efficiency, and safety.
Scalability and Efficiency
Custom metal fabrication can be adapted for small-scale prototypes and large-scale production runs. This allows manufacturers to efficiently meet market demand while maintaining consistent quality and cost-effectiveness.
Material Selection
EVs require lightweight materials to maximize energy efficiency and driving range. Customized metal fabrication enables the use of advanced alloys and composites that offer high strength-to-weight ratios, enhancing vehicle performance and safety.
Precision
Custom metal fabrication techniques — such as CNC machining, laser cutting, and 3D printing — enable manufacturers to achieve precise dimensions and tolerances. This precision is essential for creating complex components with tight specifications, ensuring they fit together seamlessly in the assembly of EVs.
Innovation and Integration
EVs incorporate advanced technologies like regenerative braking systems, electric motors, and sophisticated electronic components. Bespoke metal fabrication supports the integration of these technologies by producing housings, brackets, and structural parts that are efficiently incorporated into the vehicle’s design.
Environmental Considerations
EVs are often marketed as environmentally friendly alternatives to internal combustion engine vehicles. As such, sustainable manufacturing practices are increasingly important in their production. Custom metal fabrication techniques can minimize material waste and energy consumption, contributing to the environmental benefits of EVs.
Advanced Materials in Custom Fabrication of EVs
Here are some key materials commonly used in EV fabrication:
High-Strength Steel
Advanced high-strength steels (AHSS) are crucial for EVs due to their durability and lightweight properties. These steels are frequently used to manufacture structural components, such as chassis and safety cages, enhancing dependability and energy efficiency.
Aluminum Alloys
Aluminum alloys are widely used in EVs for their high strength-to-weight ratio and corrosion resistance. They are employed in body panels, battery enclosures, and structural components to reduce vehicle weight and improve energy efficiency and range.
Carbon Fiber Reinforced Polymers (CFRP)
CFRP materials offer exceptional strength and lightweight properties. This makes them ideal for EV components where weight reduction is critical, such as body panels, roofs, and interior components. Although more expensive than metals, CFRP can significantly improve the performance and efficiency of EVs.
Copper and Aluminum Conductors
Efficient electrical conductivity is crucial to minimize energy loss and maximize battery efficiency in EVs. Advanced copper and aluminum conductors are fabricated to ensure optimal performance of electrical systems, including wiring harnesses, busbars, and connectors.
Advanced Composites
Beyond carbon fiber, advanced composites such as fiberglass-reinforced polymers (FRP) and other hybrid materials are increasingly used in EV fabrication. They offer tailored properties such as thermal stability, impact resistance, and dimensional stability. This makes them suitable for various applications, from exterior panels to interior components.
Titanium Alloys
Titanium alloys are used in some high-performance EVs or specialized applications due to their excellent strength, corrosion resistance, and low density. They are employed in components such as battery enclosures, exhaust systems, interior and exterior trims, and chassis parts.
Innovative Fabrication Techniques
Several innovative fabrication techniques are transforming how EV components are made:
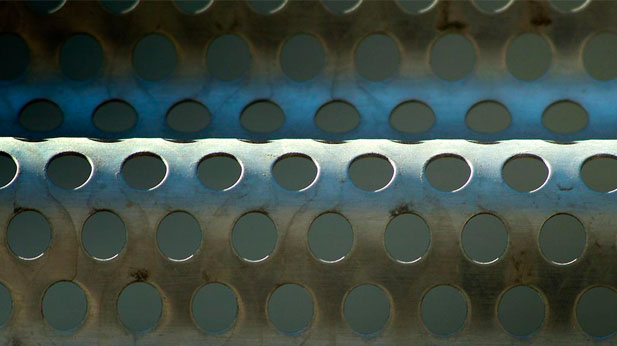
Additive Manufacturing
Additive manufacturing, commonly known as 3D printing, has emerged as a game-changer. It allows for the production of complex geometries with reduced material waste, making it ideal for prototyping and low-volume production. Components such as custom battery housings, lightweight brackets, and intricate cooling ducts can be efficiently fabricated using this technique.
Hydroforming
Hydroforming utilizes high-pressure fluid to shape metals into complex forms. This process reduces the number of components required and lowers weight while enhancing structural strength. It finds applications in producing structural components like chassis parts, frame sections, and certain body panels.
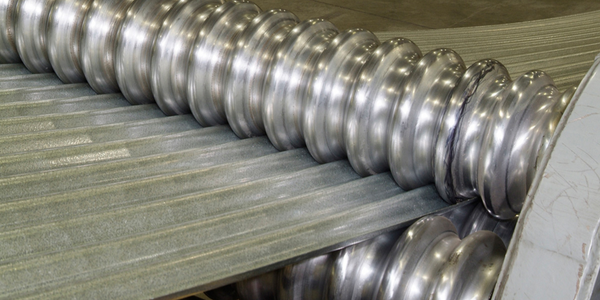
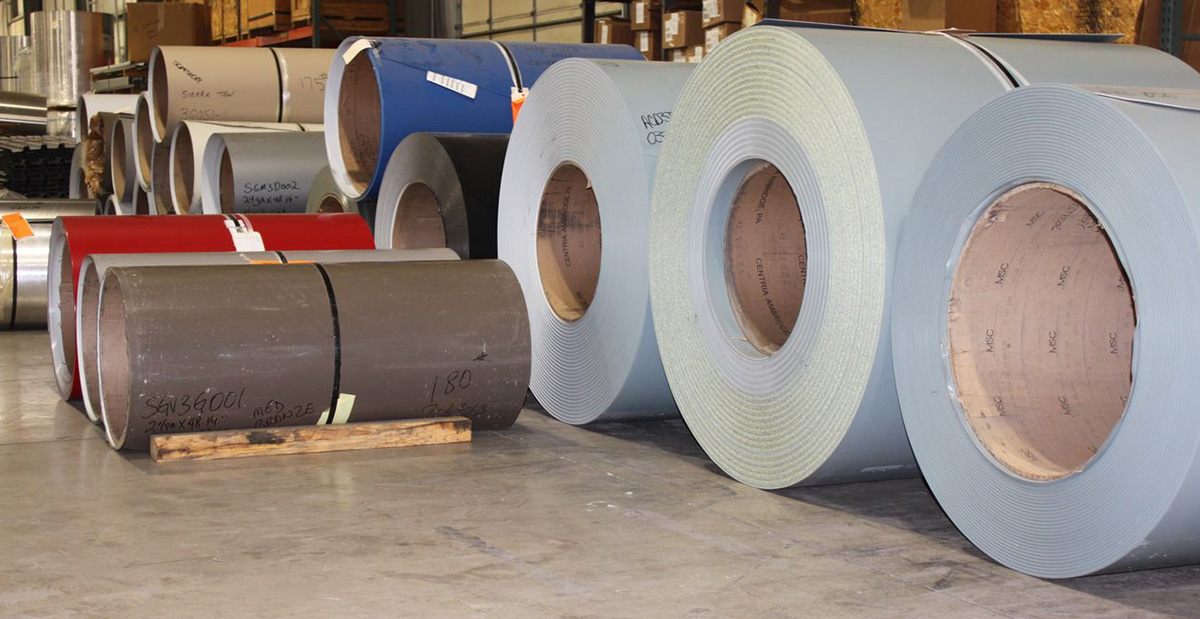
Electrochemical Machining (ECM)
ECM uses electrolysis to shape conductive materials with high precision. This technique is particularly effective for creating custom molds, specialized tooling, and components such as gears and connectors that demand exacting tolerances and intricate designs.
Friction Stir Welding (FSW)
FSW is preferred for joining materials without melting them. It produces high-strength joints suitable for EV components like battery enclosures, chassis parts, and structural reinforcements. Its ability to create robust, lightweight joints makes it indispensable in manufacturing.
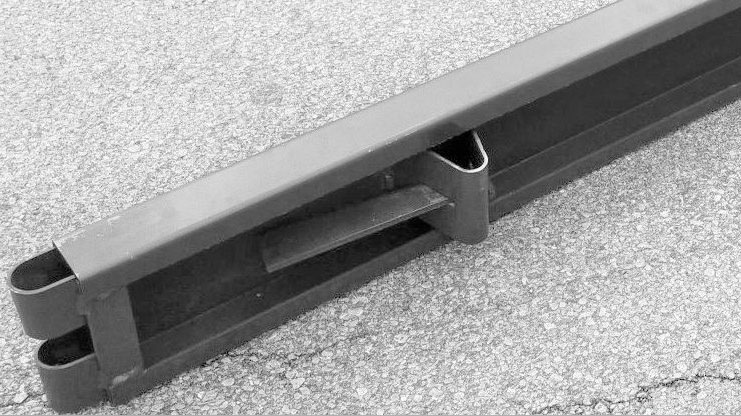
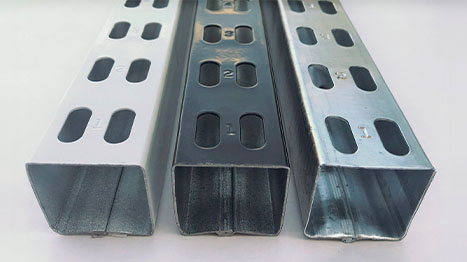
Laser Cutting
Laser cutting is crucial for fabricating precise components with minimal material waste. It provides clean, accurate cuts, while laser welding offers fast and efficient joining of components without physical contact. These techniques are widely used in assembling battery packs, fabricating body panels, and creating intricate parts requiring high accuracy and cleanliness.
Computer Numerical Control (CNC) Machining
CNC machining uses computer-guided tools to form precise metal parts. It can produce complex shapes and detailed components from various materials, including metals and plastics. This technique is used extensively in EV manufacturing to produce components such as motor housings, gearbox components, suspension parts, and precision brackets.
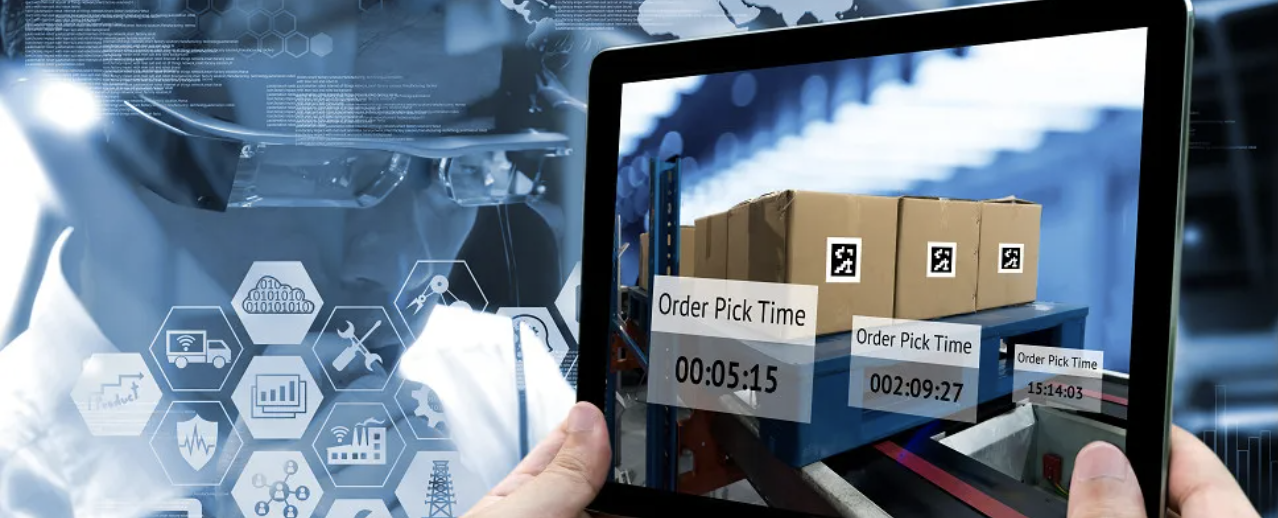
The Future of EV Manufacturing With Custom Metal Fabrication
The future of EV manufacturing is intertwined with the continued evolution of custom metal fabrication. As technology advances, so too will the capabilities of fabrication techniques, leading to even more efficient, durable, and environmentally friendly EVs.
Corrugated Metals: Trusted Manufacturer of Formed Metal Products
If you need superior custom metal fabrication solutions, look no further than Corrugated Metals! We offer an extensive range of services, including custom roll forming, press-braking, mechanical power-press operations, shearing, cut-to-length, and turret-punch operations.
We are proud to be ISO 9001:2015 registered, demonstrating our commitment to maintaining rigorous quality management systems that meet international standards. Our capabilities surpass industry standards, ensuring exceptional quality and precision in every project.
Discover how our expertise can optimize your production efficiency and product quality. Request a quote to get started today!